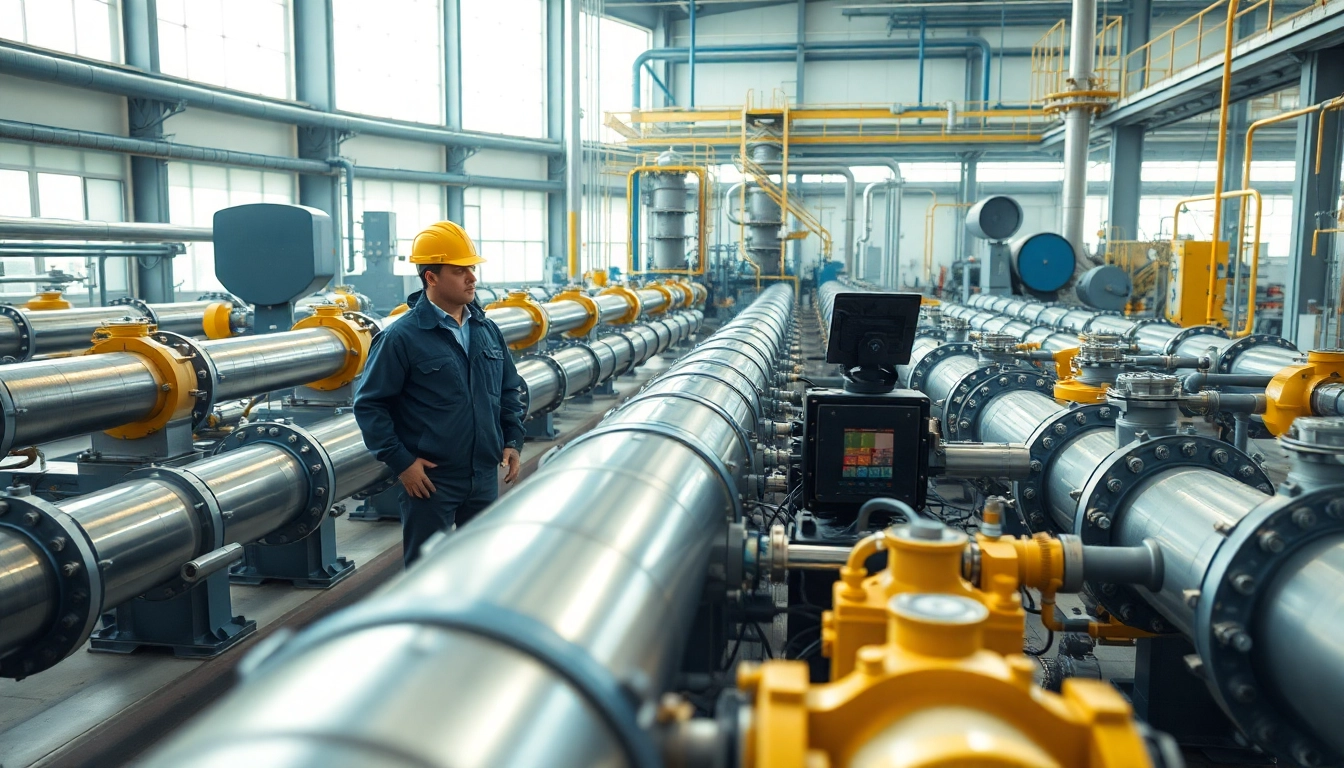
Introduction to Piping Stress in Engineering
Piping stress is a critical aspect of mechanical engineering, particularly in industries that rely heavily on piping systems, such as oil and gas, water treatment, and chemical processing. Understanding the intricacies of piping stress can help mitigate risks associated with system failures. A piping stress Company, for instance, plays a crucial role in studying these factors to optimize performance and safety.
Definition and Importance of Piping Stress
Piping stress refers to the internal and external forces acting upon a piping system. These forces can arise from internal fluid pressure, temperature variations, pipe weight, and external environmental forces. The importance of managing piping stress cannot be understated; inadequate stress analysis can lead to catastrophic failures, significant downtime, and financial losses. Engineers must ensure that systems operate within established safety margins to protect not only organizational assets but also human lives.
The Role of Piping Stress Companies in Industry
Piping stress companies are specialized firms that provide analysis, consulting, and engineering services to ensure the integrity and efficiency of piping systems. They help organizations navigate complex regulatory landscapes, implement best practices in stress analysis, and utilize advanced tools and methodologies. Their role is essential in sectors where safety and compliance are paramount, making them valuable partners in any piping-related project.
Common Misconceptions About Piping Stress
One prevalent misconception regarding piping stress is that it is a singular point of analysis. In reality, piping stress analysis is multifaceted and must consider various interacting factors. Another misconception is that only high-pressure systems require rigorous analysis. All piping systems, irrespective of pressure levels, are subject to stresses that can compromise their integrity if not adequately managed. Such misunderstandings highlight the necessity for comprehensive training and awareness in the industry.
Key Factors Affecting Piping Stress
Temperature Fluctuations and Their Impact
Temperature changes play a significant role in impacting piping stress. Materials expand and contract with temperature fluctuations, which can induce additional stress on piping systems. For instance, when hot fluids flow through pipes made of metal, the pipes expand. Ideally, expansion joints and proper anchoring can accommodate this change; however, failure to account for thermal expansion may result in misalignment, undue stress, and eventual structural failure. Engineers must meticulously account for the thermal characteristics of materials being used to ensure that their designs can withstand expected temperature variations.
Material Properties and Stress Resistance
The choice of materials greatly influences a piping system’s ability to resist stress. Common materials such as carbon steel, stainless steel, and plastic have distinct properties that dictate their performance under stress. For instance, while stainless steel demonstrates high corrosion resistance, it may also be more susceptible to stress corrosion cracking. Additionally, the yield strength, ductility, and thermal conductivity of the chosen material can either mitigate or exacerbate stress levels in piping systems. Choosing the right materials is essential for sustaining the intended service life and maintaining overall system integrity.
External Forces: Weight, Pressure, and Soil Interaction
In addition to temperature and material properties, external forces like weight, pressure, and soil interaction must be considered. As piping absorbs the weight of the fluid, its own weight, and environmental forces (such as seismic activity), the overall stress increases. In underground applications, soil conditions, including moisture levels and density, can impose additional stress on pipes. Stress analysis must incorporate these factors to predict performance accurately and ensure compliance with safety norms.
Best Practices for Piping Stress Analysis
Effective Stress Analysis Techniques
Conducting effective piping stress analysis involves various techniques, including static and dynamic analysis methods. Static analysis assesses the system under fixed variables, focusing on weight and pressure, while dynamic analysis considers motion and time, especially in systems subjected to vibrations or seismic activity. Finite element analysis (FEA) is commonly utilized in these evaluations, enabling engineers to create computational models that predict how piping systems will respond under diverse conditions. Moreover, regular inspections and re-evaluations post-installation can help identify unexpected stresses and proactively address potential issues.
Tools and Software for Accurate Measurements
Modern engineering relies heavily on software tools that assist in the accurate modeling and analysis of piping systems. Software like AutoPIPE, CAESAR II, and ANSYS provides users with capabilities to simulate stress scenarios and optimize designs accordingly. These technologies enable engineers to visualize stress distributions, pinpoint critical areas prone to failure, and test various material choices and configurations before physical implementation. Integrating technology not only enhances accuracy but also speeds up the analysis process, reducing potential turn-around times for projects.
Case Studies: Successful Piping Stress Management
Effective piping stress management can be illuminated through various case studies. For instance, a petrochemical plant faced repeated failures in its piping system due to unaccounted thermal expansion. After engaging a specialized piping stress company, a comprehensive analysis including stress simulations and re-engineering of expansion joints was conducted. This proactive approach led to a significant reduction in downtime and maintenance costs, proving that recognizing and addressing piping stress early on can save substantial resources in the long run. Another case involved a power plant where improper stress analysis led to pipe ruptures. Implementing rigorous assessment methods and material evaluations resulted in a redesign of critical piping paths, ultimately improving reliability and safety.
Challenges Faced by Piping Stress Companies
Regulatory and Compliance Issues
Piping stress companies must navigate an intricate landscape of regulatory and compliance challenges. Different industries and regions impose specific regulations concerning material selection, stress tolerances, and system designs. Keeping up-to-date with these regulations requires continuous education and adaptation. Failure to comply can not only lead to fines but may also compromise project viability. Therefore, companies must ensure their teams are well-versed in applicable regulations and standards, such as ASME B31.3 for process piping.
Balancing Cost and Accuracy in Stress Analysis
Another significant challenge is balancing the costs associated with accurate stress analysis against project budgets. On one hand, thorough analyses involving advanced modeling tools can be pricey and may influence overall project costs; on the other hand, cutting corners may lead to disastrous failures. Companies must highlight the importance of investing in quality stress analysis through education for project stakeholders and technical justification for proposed budgets. Demonstrating potential ROI through examples of cost savings from effective stress management is one way to advocate for appropriate resource allocation.
Innovation in Piping Stress Solutions
The ever-evolving landscape of piping solutions presents both challenges and opportunities. Companies need to stay at the forefront of innovations related to material technology, analysis methods, and regulatory practices. Research into advanced composite materials, for instance, could reduce the corrosion-related stresses previously experienced with traditional piping materials. Innovations in predictive modeling, such as the adoption of artificial intelligence (AI) tools, can drastically enhance the accuracy of stress predictions. Adapting to these changes, while managing traditional stress factors, will characterize the success of piping stress companies in the coming years.
Future Trends in Piping Stress Management
Advancements in Material Technologies
Future trends in piping stress management will undoubtedly be influenced by advancements in material technologies. Research is increasingly focused on the development of high-performance materials that offer improved corrosion resistance, enhanced strength-to-weight ratios, and better stress tolerance. For instance, materials like cross-linked polyethylene (PEX) and high-density polyethylene (HDPE) are becoming popular for their inherent flexibility and corrosion resistance. Adopted wisely, these advancements can lead to a shift in traditional engineering paradigms, where new materials optimize longevity and reduce maintenance requirements.
Emerging Software Innovations
With the rising complexity of piping systems, emerging software innovations will significantly enhance stress analysis capabilities. Cloud-based modeling applications can facilitate real-time collaboration among engineers, reducing miscommunication and errors due to geographical barriers. Moreover, the integration of machine learning algorithms can help analyze past failures leading to predictive modeling that anticipates stress conditions before they occur. This proactive approach shifts the balance from reactive measures to preventative maintenance, ushering in a new era of piping system management.
The Role of Sustainability in Piping Systems
As industries shift towards more sustainable practices, the role of piping systems in environmental sustainability is receiving increased focus. Emphasizing energy efficiency, waste reduction, and lifecycle assessments in piping system designs can significantly lower a project’s carbon footprint. Companies engaged in piping stress management must adopt sustainability considerations into their analysis processes, exploring options like energy-efficient systems or leveraging renewable resources. This not only ensures compliance with emerging environmental regulations but also meets the growing demand from consumers for sustainable business practices.