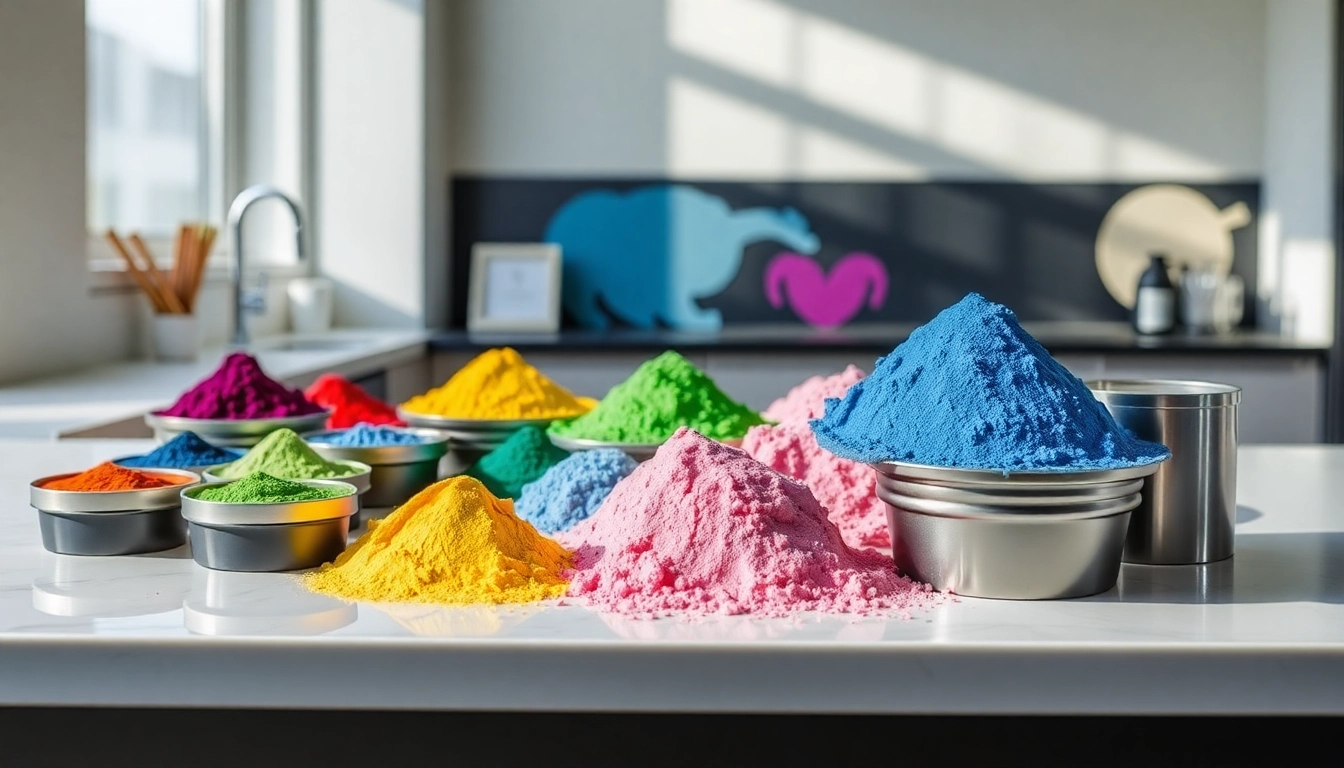
Understanding Powder Coating Basics
What is Powder Coating?
Powder coating is a modern finishing process that applies a dry powder to a surface, typically metal. Unlike traditional liquid paints that require solvents, powder coating uses polymer resins combined with curatives, pigments, leveling agents, and flow modifiers. These ingredients allow the powder to be stored and shipped without liquid carriers, making it eco-friendly and reducing volatile organic compounds (VOCs) emissions. The powder is electrostatically charged and applied to the surface. This encourages an even coating, which is then heated to melt the powder, creating a tough, uniform finish. Powder coating not only enhances the aesthetic appeal but also improves durability and resistance to various environmental factors.
The Powder Coating Process Explained
The powder coating process involves several crucial steps:
- Preparation: The substrate must be thoroughly cleaned to remove any impurities, oils, or old finishes. This is usually done through methods like sandblasting, chemical cleaning, or ultrasonic washing.
- Application: The powder is applied using an electrostatic spray gun. The gun imparts a positive charge to the powder particles, which are then attracted to the grounded metal surface, ensuring an even layer.
- Curing: The coated piece is placed in a curing oven where heat (typically between 350°F to 400°F) melts the powder, allowing it to flow and fuse together, creating a dense coating. This process usually takes 10 to 30 minutes.
- Cooling: After curing, the finished product is allowed to cool. As it cools, the coating hardens and adheres permanently to the substrate.
Common Applications for Powder Coating
Powder coating is versatile and widely used across various industries, including:
- Aerospace: Used for both decorative and protective finishes on various components, enhancing durability against harsh conditions.
- Automotive: Commonly applied to wheels, frames, and other metal parts to provide a resilient and attractive finish.
- Appliances: Found on household appliances such as refrigerators and washing machines, offering protection and aesthetic appeal.
- Furniture: Used on outdoor furniture to withstand weather conditions while retaining bright colors.
Benefits of Powder Coating
Durability and Resistance
One of the primary reasons for choosing powder coating is its unmatched durability. It provides a hard finish that is resistant to chipping, scratching, fading, and wearing. Additionally, powder-coated surfaces can withstand harsh weather conditions, making them ideal for outdoor applications. The thickness of the coating can also be controlled, allowing for a more robust protection layer compared to liquid paint.
Environmental Benefits
Powder coating is considered a green technology due to the lack of solvents and low VOC emissions. This not only makes it favorable for compliance with environmental regulations but also minimizes air pollution and health risks associated with traditional paints. Additionally, excess powder can be recycled and reused in the process, reducing waste and making it cost-effective.
Cost-Effectiveness Compared to Painting
Though the initial setup for powder coating may be higher than traditional painting techniques, the long-term cost benefits are significant. The durability and resilience of powder coating reduce the need for frequent maintenance and repainting. Moreover, the ability to apply coatings quickly and efficiently allows for lower labor costs and faster turnaround times.
Types of Powder Coatings
Polyester vs. Epoxy Powder Coating
Choosing between polyester and epoxy powder coatings can significantly impact the performance of a coated product. Polyester powder coatings are generally more UV resistant and suitable for outdoor applications as they maintain color and gloss over time. Epoxy powders offer excellent corrosion resistance and are typically used for indoor applications where exposure to sunlight is limited. Understanding the environmental conditions and usage of the coated products is essential in selecting the appropriate coating type.
Architectural and Industrial Applications
Architectural powder coatings prioritize aesthetics along with performance, used for items like window frames, railings, and facades. These coatings typically come in various finishes and colors to satisfy design specifications while ensuring consistent performance over time. On the other hand, industrial powder coatings are designed to meet the rigorous demands of manufacturing environments, such as heavy machinery, automotive parts, and equipment that require high durability and resistance to chemicals.
Custom Powder Coating Options Available
Many companies offer custom powder coating options, allowing clients to choose from a variety of colors, finishes, and textures. From metallics and gloss finishes to matte and textured coatings, customization can enhance the design and branding of various products. Additionally, manufacturers can create bespoke formulations tailored to specific operational requirements, enhancing both appearance and performance.
How to Choose a Powder Coating Service
Evaluating Quality and Expertise
When selecting a powder coating service, consider the following factors:
- Experience: Look for companies with a proven track record and extensive experience in the industry.
- Equipment: Evaluate the technology and equipment used, as modern, well-maintained machinery ensures a higher quality finish.
- Certifications: Check if the service provider adheres to industry standards and holds relevant certifications.
Questions to Ask Your Powder Coating Provider
To ensure a successful partnership, consider asking the following questions:
- What types of powders do you use, and are they environmentally friendly?
- Can you provide examples of previous work or case studies?
- What is your typical turnaround time for projects?
- How do you handle surface preparation and cleaning?
Understanding Price Estimates and Quotes
Price estimates can vary widely based on the size of the project, the type of powder used, and the specifics of the application process. It is crucial to obtain detailed quotes that break down the cost of materials, preparation, application, curing, and any additional services. Comparing multiple quotes can help identify a fair price range without compromising quality.
Best Practices for Applying Powder Coating
Preparation of Surfaces
The surface preparation stage is critical to achieving a high-quality powder-coated finish. Any contaminants on the surface, such as dirt, oil, or rust, can interfere with adhesion and compromise the final result. Effective methods for surface preparation include:
- Sanding or Grinding: To remove any existing finishes, rust, or surface imperfections.
- Cleaning Solutions: Utilizing detergent and solvents to eliminate oils and dirt.
- Blast Cleaning: Using sandblasting or abrasive blasting to provide a clean and roughened surface for better adhesion.
Equipment Needed for Powder Coating
The application of powder coating requires specific equipment, including:
- Electrostatic Spray Gun: Essential for applying the charged powder evenly over the surface.
- Curing Oven: Required to melt and cure the powder to form a hard finish.
- Powder Booth: Provides a controlled environment for application, minimizing overspray and contamination.
Post-Application Care and Maintenance
Once powder coating is applied, proper care can prolong the lifespan of the coating. Consider the following maintenance tips:
- Regular Cleaning: Dust and dirt can accumulate, so a gentle wash with soap and water is recommended.
- Avoid Harsh Chemicals: Strong solvents or abrasive cleaners can damage the finish.
- Inspection for Damage: Regularly check for any chips or scratches, and consider touch-ups if necessary to maintain appearance and protection.