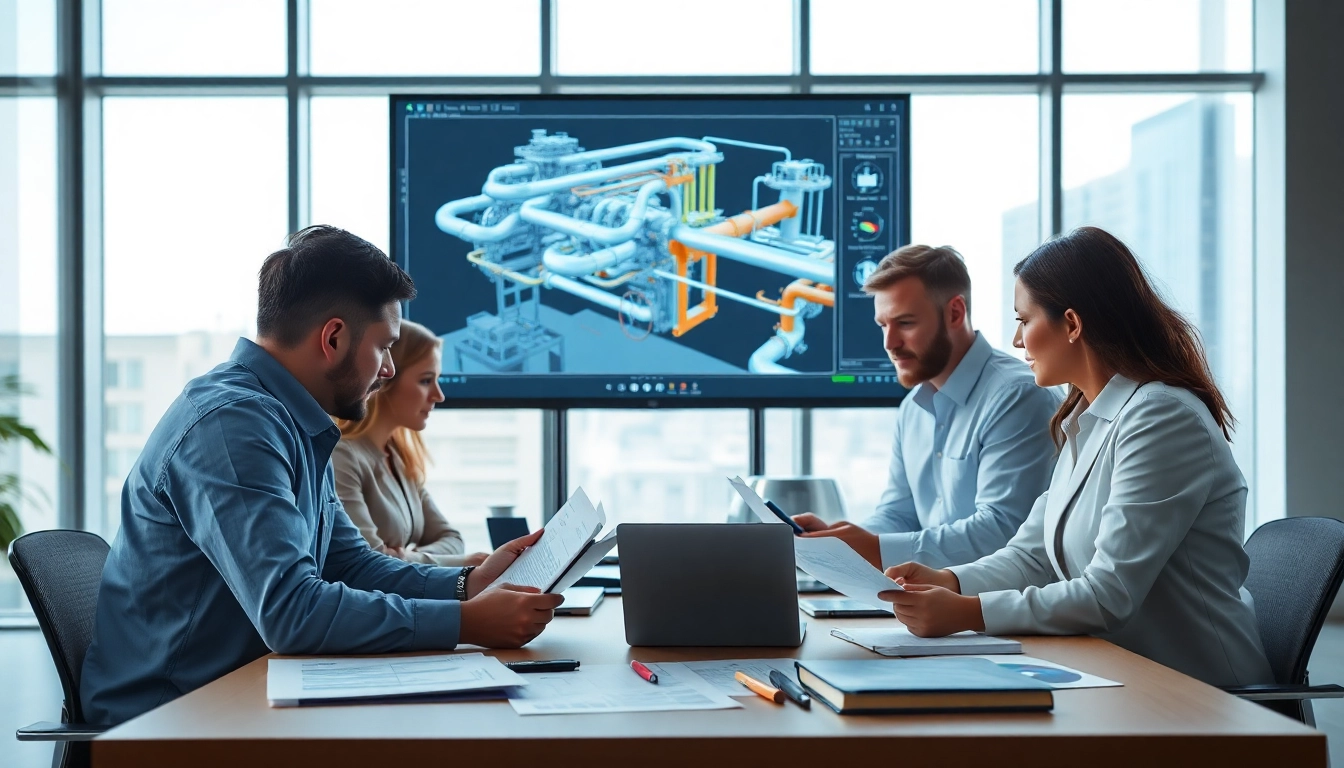
Understanding Piping Stress Analysis
What is Piping Stress Analysis?
Piping stress analysis is a critical engineering discipline that ensures the reliability and safety of piping systems used in various industries, including oil and gas, chemical processing, and power generation. At its core, piping stress analysis involves evaluating the effects of forces and moments acting on piping structures to ensure that they can withstand operational and environmental stresses without failure. This analysis encompasses thermal expansion, pressure fluctuations, supports, restraints, and any external loading conditions such as wind or seismic activity. A reputable piping stress Analysis Company is vital in executing these evaluations comprehensively, using state-of-the-art technologies and methodologies to deliver reliable solutions.
The Importance of Structural Integrity
A primary focus of piping stress analysis is maintaining structural integrity. The consequences of failing to adequately analyze piping systems can lead to catastrophic failures, resulting in significant safety risks and financial losses. Structural integrity ensures that pipes can withstand operational loads, including pressure surges and thermal expansions, thus preventing leaks, ruptures, and other forms of mechanical failure. In industries dealing with hazardous materials, ensuring integrity is not just best practice; it’s a regulatory necessity.
Common Piping Stress Analysis Methods
There are several methods employed in piping stress analysis to evaluate the stresses and strains within piping systems:
- Static Analysis: This method evaluates stresses under constant loads and conditions, ideal for initial design approval.
- Dynamic Analysis: This considers time-dependent forces, such as seismic and impact loads, which may affect piping systems during sudden events.
- Thermal Stress Analysis: Here, the effects of temperature changes and thermal expansion are analyzed, essential for high-temperature installations.
- Finite Element Analysis (FEA): A sophisticated computational technique that allows for detailed stress analysis across complex geometries, providing more accurate results than simplified calculations.
Key Factors in Piping Stress Analysis
Material Properties and Their Implications
The choice of material directly impacts the performance and durability of piping systems. Different materials exhibit distinct mechanical properties, including yield strength, ductility, and thermal expansion coefficients. Understanding these properties is essential in selecting the appropriate material for specific applications. For example, carbon steel may be adequate for low-pressure and lower-temperature operations, while specialized alloys might be necessary for extreme conditions, such as those found in petrochemical processes.
Temperature Effects on Piping Systems
Temperature fluctuations can induce significant stresses within piping systems, leading to potential failure. Consideration must be given to both ambient temperatures and operational temperatures, as these can affect material properties and the amount of thermal expansion that occurs. Engineering design must accommodate thermal expansion through proper support designs and expansion joints to mitigate stress concentrations.
Load Types: Internal vs. External
In piping stress analysis, it is crucial to differentiate between internal and external loads. Internal loads primarily consist of pressure forces exerted by the fluid contained within the pipe, while external loads could include weight from insulation, other attached equipment, or environmental factors like seismic or wind loads. Accurate assessment of all these types of loads is essential to avoid failure due to overstressing.
Tools and Technologies for Effective Analysis
Software Solutions for Piping Stress Analysis
The advent of advanced software tools has revolutionized the approach to piping stress analysis, enabling engineers to perform complex computations and visualizations that were previously cumbersome. Industry-standard software like CAESAR II, AutoPIPE, and ANSYS provide capabilities for both static and dynamic analyses, allowing for the simulation of real-world conditions that pipes would face. These tools reduce the chances of human error while enhancing the accuracy of predictions regarding pipe behavior under various conditions.
Utilizing Finite Element Analysis (FEA)
Finite Element Analysis (FEA) is a mathematical approach used in engineering to predict how structures behave under different conditions. By dividing the piping system into smaller, manageable parts (or finite elements), FEA allows for a detailed assessment of stress distribution throughout the system. This method is particularly useful for analyzing complex geometries and load scenarios, making it a frequent choice among leading piping stress analysis companies.
Innovative Tools in the Industry
Beyond traditional software, the industry is seeing an influx of innovative tools that incorporate modern technologies such as artificial intelligence (AI) and machine learning. These advancements aim to enhance predictive capabilities, automate routine assessments, and optimize design processes. Emerging tools are also enabling more seamless integration of various elements in piping systems, including better modeling of interactions between different components.
Best Practices for Piping Stress Analysis
Conducting Comprehensive Evaluations
A holistic approach to piping stress analysis begins with comprehensive evaluations that encompass all aspects of the system. This includes reviewing plant layouts, creating detailed models that incorporate all environmental factors, and subsequently performing exhaustive analyses under varied scenarios. Collaborating across disciplines—mechanical, civil, and electrical engineering—ensures comprehensive coverage of all potential risks.
Implementing Safety Standards
Safety standards such as those set by ASME (American Society of Mechanical Engineers) and API (American Petroleum Institute) must be integral to the analysis process. Compliance with these standards not only assures alignment with industry best practices but also safeguards worker safety and system reliability. Regular training and updates on safety protocols are vital for engineering teams involved in piping stress analysis.
Collaborating with Multidisciplinary Teams
Collaboration is paramount in the successful execution of effective piping stress analysis. Engaging a multidisciplinary team enables the integration of various perspectives and expertise, thus leading to more robust designs. Continuous communication between piping engineers, structural analysts, and mechanical engineers ensures that all potential stress factors are considered and addressed adequately.
Case Studies and Real-World Applications
Successful Projects by Leading Piping Stress Analysis Companies
Numerous case studies illustrate the successful application of piping stress analysis principles. For instance, a leading oil and gas company was tasked with designing a new refinery. By employing comprehensive stress analysis during the design phase, the team was able to mitigate high-pressure scenarios that could lead to system failures. The resulting piping system exceeded performance expectations, reduced maintenance costs, and improved overall safety.
Lessons Learned from Engineering Challenges
Engineers often encounter unexpected challenges during the implementation of piping systems. An example of this can be seen in a chemical plant where fluctuating temperatures led to unexpected stresses on their piping network. The analysis revealed that the initial design failed to account for temperature-induced expansion adequately. Corrective measures were implemented post-analysis, revising expansion joint placements, which resulted in a substantial increase in system longevity and reliability.
Future Trends in Piping Stress Analysis
The future of piping stress analysis is on the brink of transformation with advancements in technology. The integration of IoT (Internet of Things) and smart sensors within piping systems will enable real-time monitoring of stress and strain levels. Such innovations will provide data that can be analyzed to predict malfunctions before they occur, thus ushering in an era of preventive maintenance rather than reactive fixes. Moreover, as industries push for sustainability, analysis practices will increasingly focus on energy efficiency and reducing environmental impacts during both construction and operation phases.