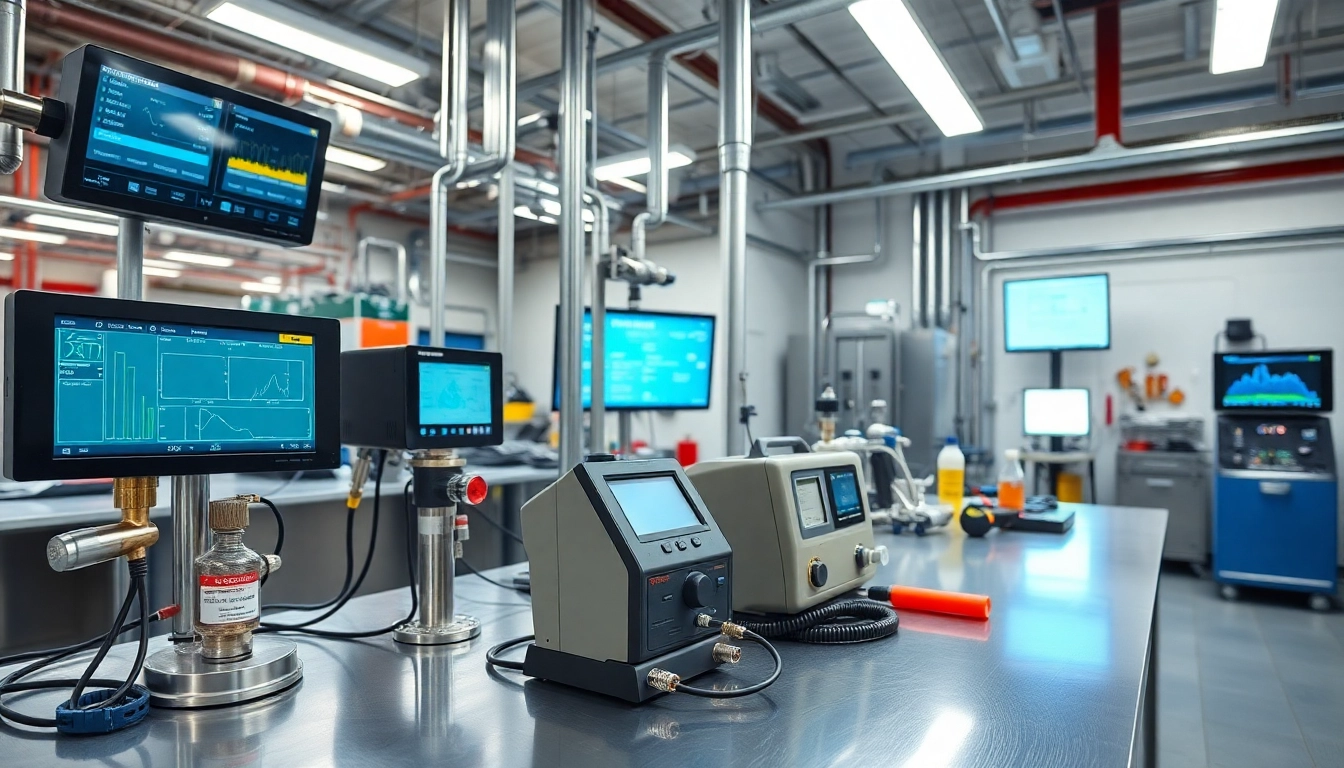
Understanding Hydrogen Detection
Hydrogen detection is an essential process across various industries, ensuring safety and compliance with regulations. With the increasing use of hydrogen in applications such as energy storage, fuel cells, and manufacturing, effective detection methods are more crucial than ever. By understanding hydrogen detection, organizations can mitigate risks, enhance safety protocols, and ensure the integrity of their operations. For comprehensive solutions and equipment related to hydrogen detection, a deeper look into the technology and methodologies involved is essential.
What is Hydrogen Detection?
Hydrogen detection refers to the methods and technologies employed to identify the presence and concentration of hydrogen gas in the air. Hydrogen, a colorless, odorless gas, poses significant safety risks due to its flammability and potential for explosion. Effective detection can prompt necessary actions to prevent accidents and ensure workplace safety.
Hydrogen detection systems typically include sensors or detectors designed specifically to sense this gas within various environments. These sensors can produce alarms or trigger safety systems when certain thresholds of concentration are reached, providing a second layer of protection for workers and facilities.
Why Hydrogen Detection Matters
The importance of hydrogen detection cannot be overstated, particularly in industrial settings where hydrogen is used or produced. Safety is the primary concern; hydrogen can quickly accumulate in enclosed spaces, creating explosive atmospheres. For professionals in sectors such as chemical manufacturing, oil and gas, and renewable energy, regularly implementing robust hydrogen detection systems is critical.
Furthermore, regulatory compliance drives the need for effective hydrogen detection. Organizations must adhere to safety standards established by bodies such as OSHA (Occupational Safety and Health Administration) and NFPA (National Fire Protection Association), which mandate specific detection protocols to protect workers and facilities from gas-related hazards.
Ultimately, the implications of neglecting hydrogen detection can be catastrophic, encompassing severe financial repercussions, legal liabilities, and threats to human life.
Common Applications of Hydrogen Detection
Hydrogen detection systems find applications across a variety of sectors:
- Chemical Manufacturing: Used during the production of chemicals. Detecting hydrogen ensures that processes remain safe and stable.
- Fuel Cell Energy: As hydrogen fuel cells grow in popularity as a clean energy source, hydrogen detection becomes vital in monitoring and managing hydrogen-produced energy systems.
- Refineries: Hydrogen is a byproduct in oil refining. Continuous monitoring is essential to manage risks associated with hydrogen as a flammable component in refining processes.
- Transport and Storage: In transportation systems, especially with hydrogen fuel vehicles and storage tanks, detection ensures that leaks are immediately identified and addressed.
- Food Industry: In modified atmosphere packaging, hydrogen is utilized to displace oxygen, and detection is crucial for quality control and safety.
Technologies Used in Hydrogen Detection
Electrochemical Sensors
Electrochemical sensors are widely used for hydrogen detection due to their high sensitivity and specificity. These sensors operate by chemically reacting with hydrogen gas, producing a measurable electronic signal. The advantages of electrochemical sensors include:
- High Precision: They provide accurate measurements of hydrogen concentrations, often down to parts per million (ppm).
- Cost-Effectiveness: Electrochemical sensors are generally more affordable and require less frequent calibration than some other technologies.
- Compact Size: Their compact design makes them suitable for various industrial applications, including handheld devices.
These sensors can be deployed in both fixed and portable applications, allowing for versatile hydrogen monitoring across environments.
Infrared and Thermal Conductivity Sensors
Infrared (IR) and thermal conductivity sensors represent another effective approach to hydrogen detection. These technologies work on different principles:
- Infrared Sensors: These detectors use infrared light to measure the absorption of specific wavelengths, which correspond to concentrations of hydrogen. They can be effective for detecting hydrogen at lower levels and in varying atmospheric conditions.
- Thermal Conductivity Sensors: These devices measure the change in thermal conductivity caused by the presence of hydrogen. As hydrogen has different thermal conductivity compared to other gases, these sensors can reliably assess concentrations.
While these sensors may require more extensive calibration and setup, they can deliver effective results in larger systems or processes where consistent hydrogen monitoring is vital.
Optical and Acoustic Technologies
Less common but emerging technologies involve optical and acoustic methods for hydrogen detection:
- Optical Sensors: By employing lasers or optical fiber, these sensors can detect changes in light properties when hydrogen is present. They can be extremely sensitive and provide real-time monitoring.
- Acoustic Sensors: These devices utilize sound waves to detect hydrogen changes in the environment, exploiting the differences in sound travel rates influenced by hydrogen concentrations.
Although these technologies are still being developed, they show great promise for high-precision requirements in hydrogen monitoring.
Best Practices for Implementing Hydrogen Detection
Site Assessment and Hazard Analysis
Before selecting and implementing hydrogen detection systems, conducting a thorough site assessment is critical. This includes evaluating potential sources of hydrogen, such as equipment, processes, and storage areas. A hazard analysis clarifies where the risks are highest, allowing for targeted detection solutions. This step should involve:
- Identifying Potential Leak Points: Understand where gas may escape or accumulate, such as joints, sealed areas, or valves.
- Typical Concentration Levels: Understand typical hydrogen concentrations within operations to set appropriate detector thresholds.
- Environmental Factors: Consider Ambient conditions such as temperature and pressure that might influence the response of detection systems.
Selecting the Right Equipment
Once the assessment and analysis are completed, selecting the appropriate monitoring equipment for hydrogen detection becomes paramount. Depending on the findings, organizations should consider:
- Type of Sensor: Choose between electrochemical, IR, thermal conductivity, or emerging technologies based on specific requirements identified during site assessment.
- Regulatory Compliance: Ensure that selected systems meet internal and external safety standards and regulations.
- Integration Capabilities: Consider equipment that can communicate with existing monitoring systems or smart infrastructures for comprehensive monitoring solutions.
Installation and Calibration Guidelines
Proper installation and calibration of hydrogen detection systems are vital for accurate and reliable performance. Following manufacturer guidelines is always recommended, but key aspects include:
- Placement: Position sensors in areas of potential hydrogen accumulation, such as elevated points, to account for hydrogen’s buoyancy.
- Regular Calibration: Schedule periodic calibration and testing to ensure sensors remain sensitive and accurate.
- Routine Training: Conduct regular training sessions for staff to ensure they can respond effectively to alerts from detection systems.
Maintenance and Compliance in Hydrogen Detection
Regular Testing and Calibration
To ensure ongoing reliability and efficiency, regular testing of hydrogen detection equipment is essential. This includes performing functional tests to ensure responsiveness and validating calibration settings. Key practices include:
- Scheduled Maintenance: Implement a maintenance plan that outlines when and how testing and calibration will take place.
- Documentation: Keep thorough records of all maintenance activities as part of compliance with occupational safety regulations.
Adhering to Safety Standards
It is critical to stay informed about safety standards and regulations from authorities such as OSHA and NFPA. These regulations specify the types of detection technologies, maintenance frequencies, installation guidelines, and necessary employee training. Failure to comply not only risks penalties but also can lead to serious accidents.
Documenting Procedures and Findings
Organizations must establish robust documentation protocols around hydrogen detection activities, which help in audits and improve operational transparency. Essential documentation includes:
- Incident Reports: Document any incidents involving hydrogen escapes or detector triggers to analyze and improve safety practices.
- Calibration Records: Maintain logs of calibration and maintenance activities to demonstrate compliance with standards.
- Training Documents: Ensure all training sessions are documented to verify that employees are up to date with protocols and safety practices.
Future Trends in Hydrogen Detection
Advancements in Sensor Technology
The field of hydrogen detection is constantly evolving, with new advancements in sensor technologies aimed at improving accuracy, reliability, and user-friendliness. Innovations may include:
- Miniaturization: Development of smaller and more portable sensors, enabling ease of use in various applications.
- Enhanced Communication Features: Integration of IoT capabilities, allowing for automated data monitoring and alert systems.
- Smart Sensors: Sensors capable of self-diagnosis and adaptation to environmental conditions for optimal performance.
Integration with Smart Building Systems
There is a growing trend toward integrating hydrogen detection systems with broader building management or smart infrastructure solutions. For instance, linking hydrogen detectors with fire alarm systems can offer synchronous safety measures. This ensures that if hydrogen levels reach hazardous thresholds, the building’s overall safety protocols can initiate responses automatically, reducing human error.
The Role of AI in Gas Detection
Artificial intelligence (AI) is expected to play a significant role in the future of gas detection systems, including hydrogen. By employing machine learning algorithms, these systems can analyze patterns within sensor data and predict potential hazards before they occur. Implementing AI can lead to:
- Improved Predictive Maintenance: Systems that can predict when a sensor might fail or need servicing, reducing downtime and ensuring reliability.
- Enhanced Decision Making: Offering insights derived from data to help operators and safety personnel make informed decisions quickly during emergencies.
The future of hydrogen detection promises innovative approaches to maintaining safety in environments where hydrogen is present. By understanding current technologies and future trends, organizations can better prepare for potential hazards involving hydrogen gas.