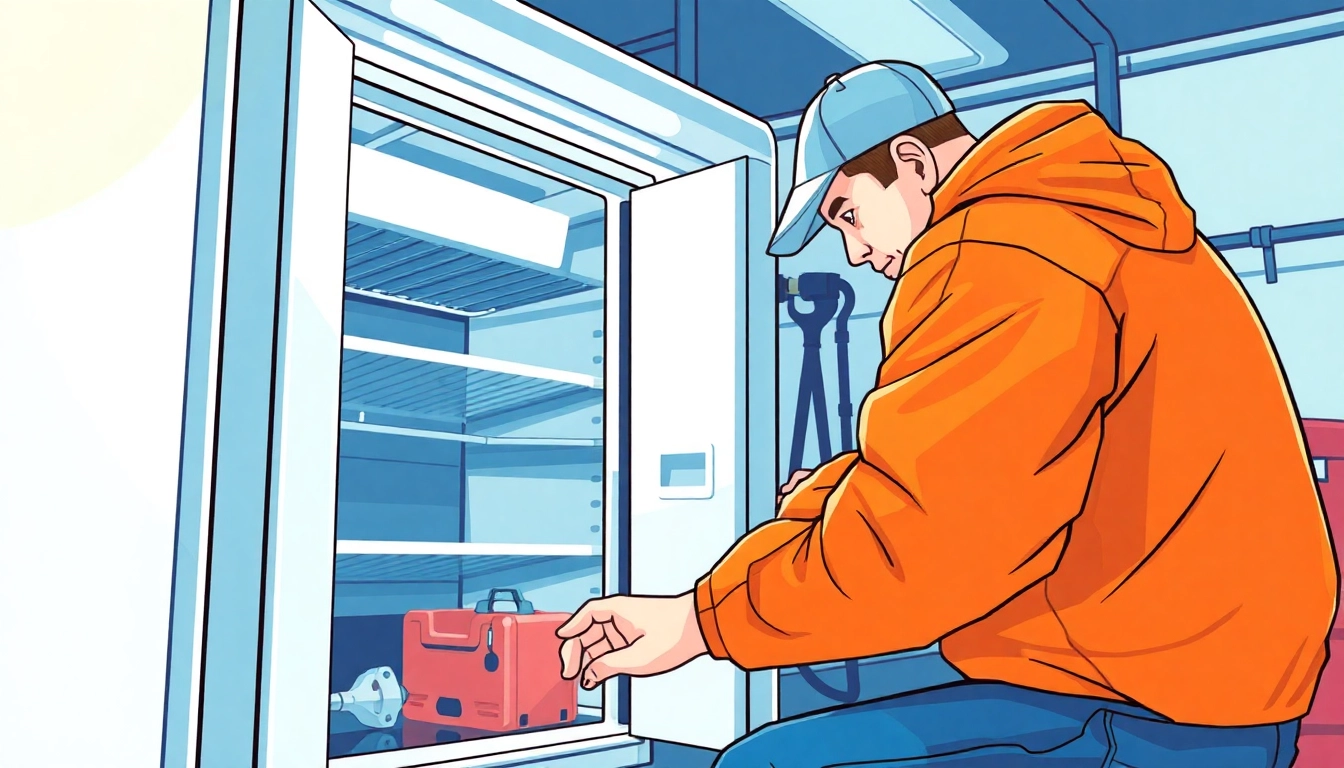
Understanding Walk In Freezer Repair
In commercial and industrial settings, walk-in freezers play an essential role in preserving food products and ensuring that they are kept at safe temperatures. However, like any piece of machinery, these units can run into problems that disrupt their operations. Understanding the fundamentals of walk in freezer repair is vital for businesses that rely on these systems. In this comprehensive guide, we will explore common issues associated with walk-in freezers, the importance of routine maintenance, and signs that indicate repair is necessary.
Overview of Common Issues
Walk-in freezers are subject to various technical issues that can impact their performance. Some of the most common problems include:
- Temperature Fluctuations: This issue often arises from faulty thermostats or malfunctioning compressors, leading to inconsistent internal temperatures.
- Compressor Failures: The compressor is the heart of any refrigeration system. If it fails, the walk-in freezer will not maintain the required cold temperatures.
- Frost Build-Up: Excessive frost can accumulate due to door leaks or frequent opening, obstructing airflow and reducing efficiency.
- Leaking Refrigerant: A drop in refrigerant levels indicates a leak, which can significantly impair the unit’s performance.
Importance of Regular Maintenance
Regular maintenance of walk-in freezers is crucial for several reasons. It not only enhances the efficiency and lifespan of the unit but also ensures compliance with health regulations. Neglecting routine checks can lead to costly repairs, potential food spoilage, and unsafe working conditions.
Preventative tasks such as cleaning condenser coils, checking door seals, and monitoring temperature logs help identify and mitigate issues before they escalate. Moreover, trained technicians possess the expertise to handle specific maintenance tasks, ensuring everything runs optimally.
Signs Your Walk In Freezer Needs Repair
Recognizing the signs of a malfunctioning walk-in freezer can save businesses from significant losses. Key indicators include:
- Strange Noises: Unusual sounds like clanking, buzzing, or hissing can signal mechanical issues or refrigerant leaks.
- High Energy Bills: If energy costs surge unexpectedly, it could mean the freezer is working harder to maintain cold temperatures due to inefficiencies.
- Unexpected Warm Spots: Warm areas within the freezer indicate airflow blockage or cooling system malfunctions.
- Condensation or Ice Buildup: Excess moisture inside the freezer may suggest door seal failures or defrost cycles that are not functioning properly.
DIY Troubleshooting Tips for Walk In Freezer Problems
Step-by-Step DIY Repairs
While professional repairs are often recommended for complicated issues, certain tasks can be performed by business owners or staff to troubleshoot minor problems. Some simple DIY steps include:
- Check the Thermostat Settings: Ensure that the thermostat is set correctly and not accidentally adjusted.
- Inspect Door Seals: Examine door gaskets for tears or dirt. Clean or replace them if necessary to maintain airtight seals.
- Clean the Condenser Coils: Dirty coils can drastically reduce the freezer’s efficiency. Unplug the unit and use a soft brush or vacuum to clean them.
- Clear the Drain Line: If there are signs of pooling water, the drain line might be blocked. Use a wet/dry vacuum to clear it.
Tools You’ll Need for Walk In Freezer Repair
When undertaking walk-in freezer repairs, having the right tools is essential. Here are some must-have tools:
- Multimeter: Used for checking electrical components and diagnosing issues.
- Refrigeration Wrench: Essential for handling refrigerant line fittings and valves.
- Screwdrivers and Pliers: Basic tools for opening panels and making minor adjustments.
- Cleaning Equipment: Brushes, vacuums, and cloths for maintenance and cleaning tasks.
When to Call a Professional
While many small repairs can be handled in-house, knowing when to call in the experts is crucial for effective problem resolution. Call a professional in cases of:
- Compressor issues or replacements
- Refrigerant leaks
- Severe electrical issues
- Complex mechanical failures
Professionals are equipped not only with the necessary tools but also with the expertise to diagnose underlying problems accurately. Leveraging their experience guarantees that repairs are performed safely and correctly.
Choosing the Right Walk In Freezer Repair Service
What to Look for in a Repair Service
Choosing the right repair service for your walk-in freezer is critical for maintaining operational efficiency. Consider these factors:
- Experience and Reputation: Look for services that have a proven track record and positive testimonials from previous customers.
- Certifications: Ensure technicians are certified to work on refrigeration systems and follow industry standards.
- Service Range: A good repair company offers comprehensive services, including installation, maintenance, and emergency repairs.
Understanding Repair Costs
Repair costs for walk-in freezers can vary greatly depending on several factors, including the nature of the problem, parts required, and labor rates. On average, businesses can expect to pay between:
- $250 to $650 for compressor repairs.
- $100 to $300 for basic maintenance and service calls.
- Higher costs for emergency service calls outside of regular business hours.
Always request a detailed quote before commencing any work. This transparency helps avoid hidden charges and ensures a more accurate budget.
Reading Reviews and Testimonials
Before finalizing a repair service, reading reviews and testimonials can provide insight into the company’s reliability and quality of work. Consider checking:
- Google reviews and local business directories.
- Online forums within the refrigeration industry for personal experiences and recommendations.
- Social media platforms where customers might share their feedback and concerns.
A company with consistently positive reviews is more likely to deliver satisfactory results and timely service.
Preventative Measures for Walk In Freezers
Regular Maintenance Checklist
Establishing a regular maintenance routine for your walk-in freezer can prevent many common issues. Here is a checklist to follow:
- Inspect and clean condenser coils every 3-6 months.
- Check door seals for integrity and cleanliness monthly.
- Monitor the temperature logs daily for any inconsistencies.
- Clean drains to prevent clogging on a quarterly basis.
- Schedule professional maintenance at least once a year.
Best Practices to Extend Lifespan
To maximize the lifespan of walk-in freezers, consider implementing these best practices:
- Limit Door Openings: Encourage staff to minimize door openings to maintain cold temperatures and reduce workload on the compressor.
- Store Products Properly: Allow for proper airflow around products to optimize cooling efficiency.
- Avoid Overloading: Do not exceed weight limits or storage capacities to prevent damage and impaired circulation.
Common Mistakes to Avoid
Taking proper care of a walk-in freezer is essential, but there are mistakes that can undermine these efforts. Avoid the following:
- Ignoring Warning Signs: Do not overlook persistent issues; they usually indicate a more significant problem.
- Neglecting Maintenance: Skipping or delaying regular maintenance can lead to more severe and costly failures.
- Using Inexperienced Technicians: Avoid hiring unqualified personnel, as they may inadvertently cause more damage.
Advanced Solutions for Walk In Freezer Repair
Upgrading Your Freezer System
In some cases, upgrading components of your walk-in freezer can be a more cost-effective solution than continual repairs. For instance, investing in energy-efficient refrigeration systems can lead to lower operating costs over time. Additionally, incorporating smart monitoring systems can provide real-time data on temperature and humidity, assisting in proactive maintenance.
Energy Efficiency Considerations
Energy efficiency is an increasingly important factor in walk-in freezer operations, especially given rising energy costs. Some strategies to improve energy efficiency include:
- Upgrading to LED lighting inside the freezer.
- Installing automatic door closers to minimize cold air loss.
- Incorporating energy-efficient insulation materials.
Future-Proofing Your Walk In Freezer
To future-proof your walk-in freezer, it’s essential to anticipate changes in regulations, technology, and operational needs. Sticking with cutting-edge technology and ensuring the system can accommodate upgrades in the future will benefit your operation in the long run. Engaging with seasoned professionals for advice on the best practices regarding equipment choices and sustainable practices can further enhance your approach.