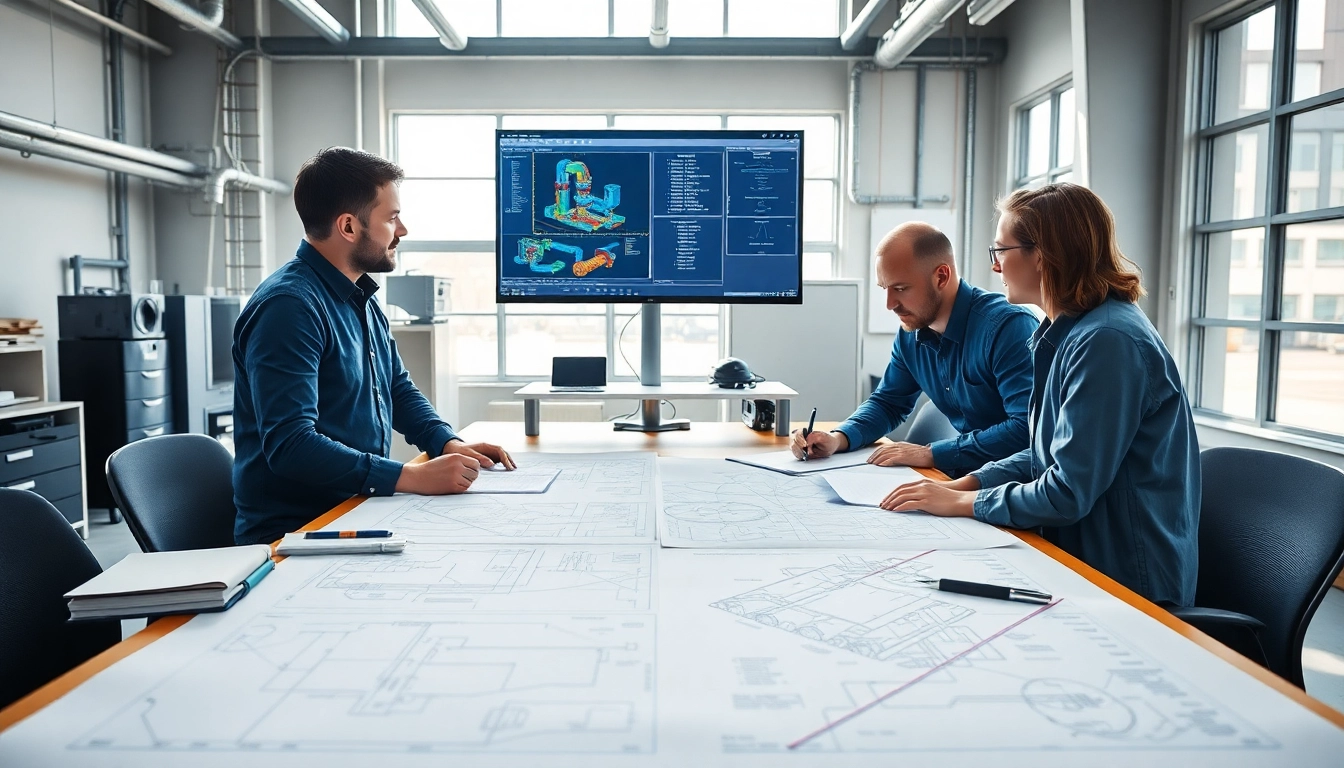
Understanding Pipe Stress Analysis
In engineering, particularly in the fields of piping and mechanical systems, pipe stress analysis plays a crucial role in ensuring the integrity and safety of piping systems. This involves a systematic assessment of how pipes will react to varying loads, thermal changes, and operational stresses. Engaging a qualified pipe stress Company is vital for effective design and installation. Correct execution of this analysis can prevent catastrophic failures, minimize downtime, and increase the overall efficiency of operations.
What is Pipe Stress Analysis?
Pipe stress analysis refers to the evaluation of piping systems under various conditions and loading scenarios. This includes internal fluid pressure, external loads, and temperature-induced expansion and contraction. The primary objectives of this analysis are to determine the stress levels induced in the pipe and to ensure that they are within safe limits specified by industry standards.
During the analysis process, engineers utilize a combination of theoretical calculations and industry-standard software to model the behavior of piping systems. The results help in identifying potential issues before they occur in real-world scenarios.
Importance of a Pipe Stress Company
A specialized pipe stress company brings expert knowledge and tools to the table, which enhances the safety and reliability of piping designs. Without thorough stress analysis, pipes may be subject to undue stress that can lead to bending, buckling, or even rupture over time.
Moreover, engaging experienced professionals in this niche significantly reduces the risk of design non-compliances with regulatory standards, such as ASME B31.1 for power piping or B31.3 for process piping.
Key Principles of Pipe Stress Measurement
The principles of pipe stress measurement include an understanding of static and dynamic loads, factors affecting stress levels, and the resultant strains on different materials used in piping. Some key factors include:
- Temperature Effects: Changes in temperature cause expansion and contraction of materials, which must be factored into the design.
- Support Locations: The placement of supports can significantly affect stress distribution and must be optimized for each system.
- Material Properties: Different materials exhibit varying stress responses under load; knowing these properties is crucial.
Methods and Tools Used by Pipe Stress Companies
Software Applications for Analysis
The advancement of technology has revolutionized pipe stress analysis, making it more accurate and efficient. Several software applications are employed, including:
- CAESAR II: Widely used for pipe flexibility analysis, offering comprehensive modeling capabilities.
- AutoPIPE: Allows for enhanced modeling of dynamic loads in piping systems.
- ROHR2: A flexible tool that provides detailed stress analysis results for complex piping layouts.
Manual vs. Automated Analysis Techniques
While automated software analysis is more common today due to its speed and accuracy, manual calculations still play a role, especially in preliminary assessments or smaller-scale projects. Manual methods often rely on fundamental engineering principles and are useful for teaching and understanding the basis of stress analysis.
Case Studies of Effective Tool Utilization
Consider a recent project where an industrial plant underwent a major overhaul of its piping system. By utilizing CAESAR II, engineers identified critical stress points that would have otherwise been overlooked. Adjustments in support locations and pipe routing ultimately saved the company significant costs associated with downtime and repairs.
Best Practices in Pipe Stress Engineering
Design Considerations for Stress Management
Effective stress management begins in the design stage. Key practices include:
- Utilizing appropriate materials that can handle specific temperatures and pressures.
- Incorporating sufficient flexibility in pipe design to accommodate thermal expansion.
- Strategic placement of expansion joints and supports to alleviate stress concentrations.
Ensuring Compliance with Industry Standards
Staying up to date with the latest industry standards is crucial. Compliance with ASME codes not only enhances safety but also contributes to project approval and client satisfaction. Regular training and certification of engineers in the latest standards is recommended to maintain compliance.
User Recommendations for Optimal Results
When working with pipe stress companies, clear communication is vital. Clients should provide detailed operational parameters and any anticipated changes that might arise over the lifespan of the system. Regular reviews and adjustments to the stress analysis can also help in maintaining optimal performance.
Common Challenges in Pipe Stress Analysis
Identifying Potential Structural Failures
One of the primary challenges in pipe stress analysis is identifying potential failure points. Structural failures can lead to catastrophic events, thus requiring an ongoing assessment of all aspects of the piping systems. Some common techniques for identifying these points include:
- Using software simulations to predict stress under extreme conditions.
- Physical inspections combined with analytical assessments to ensure compliance.
- Implementing non-destructive testing (NDT) methods to gauge unseen issues.
Resolving High Secondary Stresses
High secondary stresses can arise from various factors including inadequate support, thermal expansion, and changes in operating conditions. Addressing these stresses often requires internal adjustments such as re-evaluating support placement or modifying pipe routing to distribute loads more evenly.
Mitigation Strategies and Solutions
A multi-faceted approach is typically required to mitigate the risks associated with pipe stress analysis. Solutions might include:
- Increasing the frequency of inspections to catch issues early.
- Revamping design parameters based on the latest analytical methods.
- Employing materials with higher resistance to stress and temperature changes.
The Future of Pipe Stress Companies
Emerging Technologies in Stress Analysis
The future of pipe stress analysis is promising with advancements in technologies like machine learning and big data analytics, which allow for predictive analyses and real-time monitoring. These technologies will help engineers anticipate stress points and respond proactively.
Trends Impacting the Engineering Industry
Some trends anticipated to influence the pipe stress analysis sector include greater collaboration across disciplines, increased focus on sustainability, and the integration of virtual and augmented reality in training and simulation environments. Cross-disciplinary collaborations help engineers understand the impact of stress analysis on overall project success.
The Role of Sustainability in Engineering Practices
Sustainability is gaining prominence as projects strive to minimize environmental impact. Using sustainable materials and considering lifecycle impacts during stress analysis will become integral practices in the future. Understanding the environmental compliance issues will be essential for the future roles of pipe stress companies.