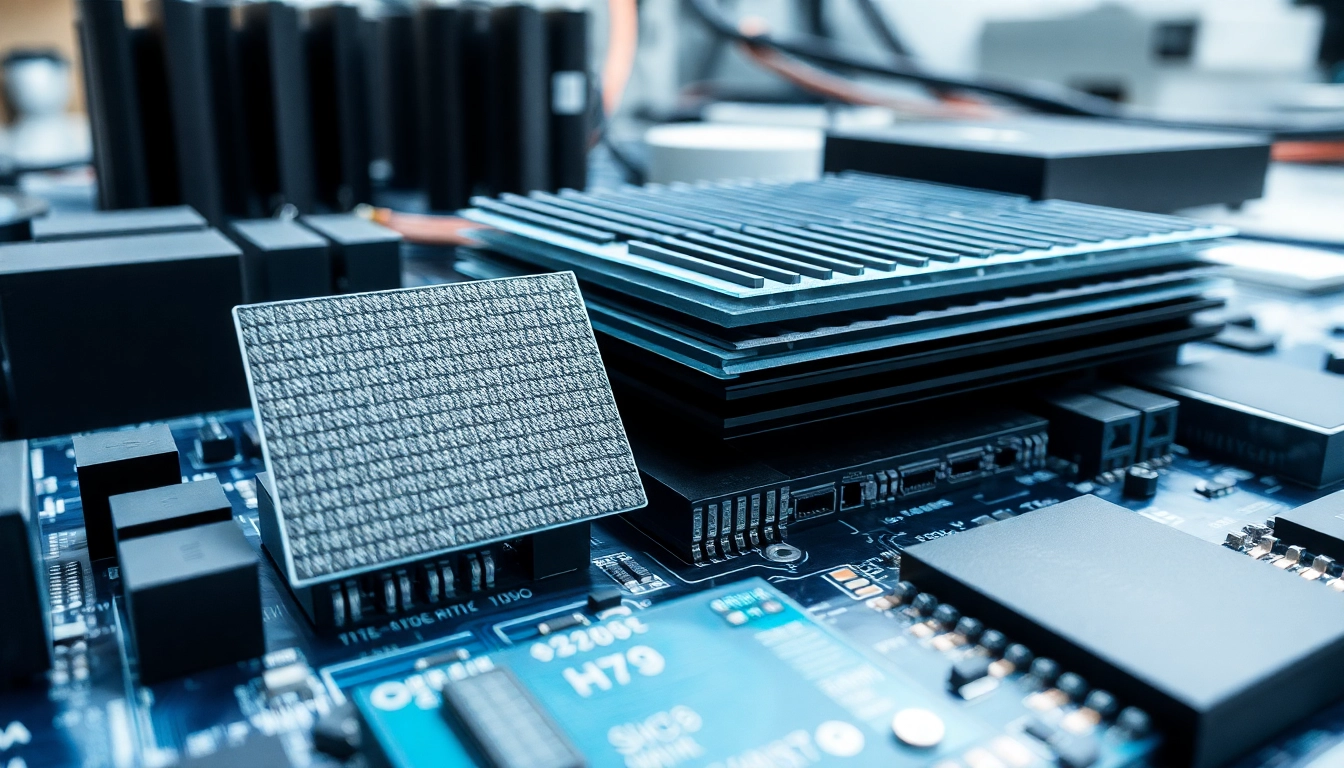
Introduction to Thermal Management Materials
As electronic devices continue to evolve and become more powerful, effective thermal management solutions have become imperative for their optimal performance and longevity. At the core of this technology are thermal management materials. These materials serve crucial functions in regulating temperature and dissipating excess heat generated by electronic components, thereby preventing failures and enhancing operational efficiency. This article explores the types, applications, and design considerations surrounding thermal management materials, providing comprehensive insights into their roles in modern electronics.
What Are Thermal Management Materials?
Thermal management materials are a diverse array of products developed explicitly to regulate the flow of heat and ensure optimal temperatures in electronic devices. They facilitate thermal conduction, dissipation, and insulation in various applications, minimizing the risk of overheating and damage to sensitive components. Examples of thermal management materials include thermal interface materials (TIMs), thermal pads, adhesives, and gels, each engineered to meet specific thermal management needs.
Importance of Thermal Management in Electronics
In the realm of electronics, proper thermal management is not just beneficial but crucial for several reasons:
- Enhanced Performance: Heat can impede the function of electronic components, leading to decreased performance. Effective thermal management ensures that devices operate within acceptable temperature ranges.
- Increased Lifespan: Excessive heat accelerates wear and tear on electronic components. By mitigating thermal buildup, thermal management materials can extend the lifespan of devices.
- Reliability and Safety: Overheated electronics are prone to failure, which can pose safety risks. Effective heat dissipation can prevent such hazards, ensuring reliability in performance.
Overview of Common Types of Thermal Management Materials
Various types of thermal management materials, each with its unique properties and uses, play integral roles in heat management. The primary categories include:
- Thermal gap pads
- Thermal adhesives
- Thermal greases
- Thermal gels
Types of Thermal Management Materials
Thermal Gap Pads: Features and Benefits
Thermal gap pads, often made from silicone or polymer composites, are used to fill small gaps between heat sources and heat sinks. They improve heat transfer even in irregularly shaped surfaces. The benefits of gap pads include:
- Soft and Flexible: These pads conform well to surfaces, ensuring maximum contact area for heat transfer.
- Thermal Conductivity: High thermal conductivity ratings make them effective in dissipating heat quickly.
- Electrical Insulation: Most thermal gap pads also act as electrical insulators, reducing the risk of short circuits.
Thermal Adhesives as Interface Materials
Thermal adhesives bond components together while providing thermal conductivity. These adhesives are essential when mechanical joining methods are either impractical or insufficient. Key advantages include:
- Strong Bonds: They provide robust adhesion, ensuring that components remain securely in place even under thermal stress.
- Speed of Application: The curing process is usually quick, allowing for faster production timelines.
- Custom Formulations: Thermal adhesives can be tailored for specific applications, offering varying levels of thermal conductivity and viscosity.
Thermal Greases and Their Applications
Thermal greases are viscous substances applied between surfaces to enhance thermal conductivity. They are particularly effective where metal-to-metal contact occurs, such as between a CPU and a heat sink. Features and advantages include:
- High Thermal Conductivity: Specialized formulations provide excellent heat dissipation characteristics.
- Easy Application: Greases are easy to apply, allowing for precise control over the amount used.
- Removability: They can be easily removed and reapplied, making maintenance straightforward.
Applications of Thermal Management Materials
Usage in Consumer Electronics
In consumer electronics, efficient thermal management is vital for improving the user experience and device longevity. Products such as smartphones, laptops, and gaming consoles benefit from thermal materials that keep critical components cool. For instance, thermal pads are commonly used in smartphones to protect processors and prevent overheating during extensive use.
Role in Automotive Applications
Automotive manufacturers increasingly rely on thermal management materials in electric vehicles (EVs) and traditional combustion engines. Heat plays a crucial role in performance and safety in vehicles, particularly with battery systems managing high levels of heat. Applications include:
- Thermal interface materials in battery packs to ensure efficient heat transfer.
- Ventilation systems utilizing thermal gap fillers to maintain component temperatures.
- Use of thermal adhesives for securing heat sinks and improving reliability.
Impact on Industrial Equipment Efficiency
Thermal management is essential in industrial settings where high-performance machinery operates at elevated temperatures. The proper application of thermal materials can lead to:
- Improved Efficiency: Maintaining optimal temperatures can enhance machine efficiency and performance.
- Reduced Maintenance Costs: Proper thermal management decreases wear and tear, resulting in lower maintenance costs.
- Safety Enhancements: Minimizing overheating can lead to a safer working environment.
Design Considerations for Thermal Management
Choosing the Right Thermal Management Materials
Selecting appropriate thermal management materials involves careful consideration of various factors, including:
- Thermal conductivity requirements
- Application environment (temperature and humidity)
- Mechanical properties (adhesion strength and flexibility)
- Electrical insulation needs
Factors Influencing Material Selection
Several factors can influence the selection of thermal management materials:
- Device Purpose: Different applications may require different thermal properties (e.g., high performance vs. low-cost solutions).
- Regulatory Compliance: Materials must meet specific safety and environmental standards in certain industries, such as automotive or aerospace.
- Cost Considerations: Budget constraints can dictate material choices, particularly for mass production.
Best Practices for Implementation
When implementing thermal management materials, it is essential to follow best practices to optimize performance:
- Ensure clean surfaces for optimal adhesion.
- Apply materials evenly to avoid air gaps that can act as thermal barriers.
- Regularly monitor and maintain thermal interfaces to ensure continued efficacy over time.
Future Trends in Thermal Management Materials
Innovations in Thermal Interface Materials
The landscape of thermal management materials is constantly evolving, driven by advancements in material science. Innovations include:
- Nanomaterials that enhance thermal conductivity while reducing weight.
- Phase change materials (PCMs) that store and release heat as they change states, offering dynamic temperature regulation.
- Advanced polymers designed for extreme thermal conditions in harsh environments.
Impact of Regulations and Standards
As industries focus on sustainability and safety, regulations surrounding thermal management materials are expected to tighten. Compliance with standards such as RoHS and REACH will become increasingly important, influencing material development and selection processes.
Market Trends and Projections for Thermal Solutions
The market for thermal management materials is projected to grow significantly over the next few years, influenced by trends such as:
- The rising demand for efficient thermal solutions in consumer electronics and automotive sectors.
- Technological advancements that enable the development of high-performance materials.
- Increasing focus on energy efficiency and sustainability in manufacturing practices.