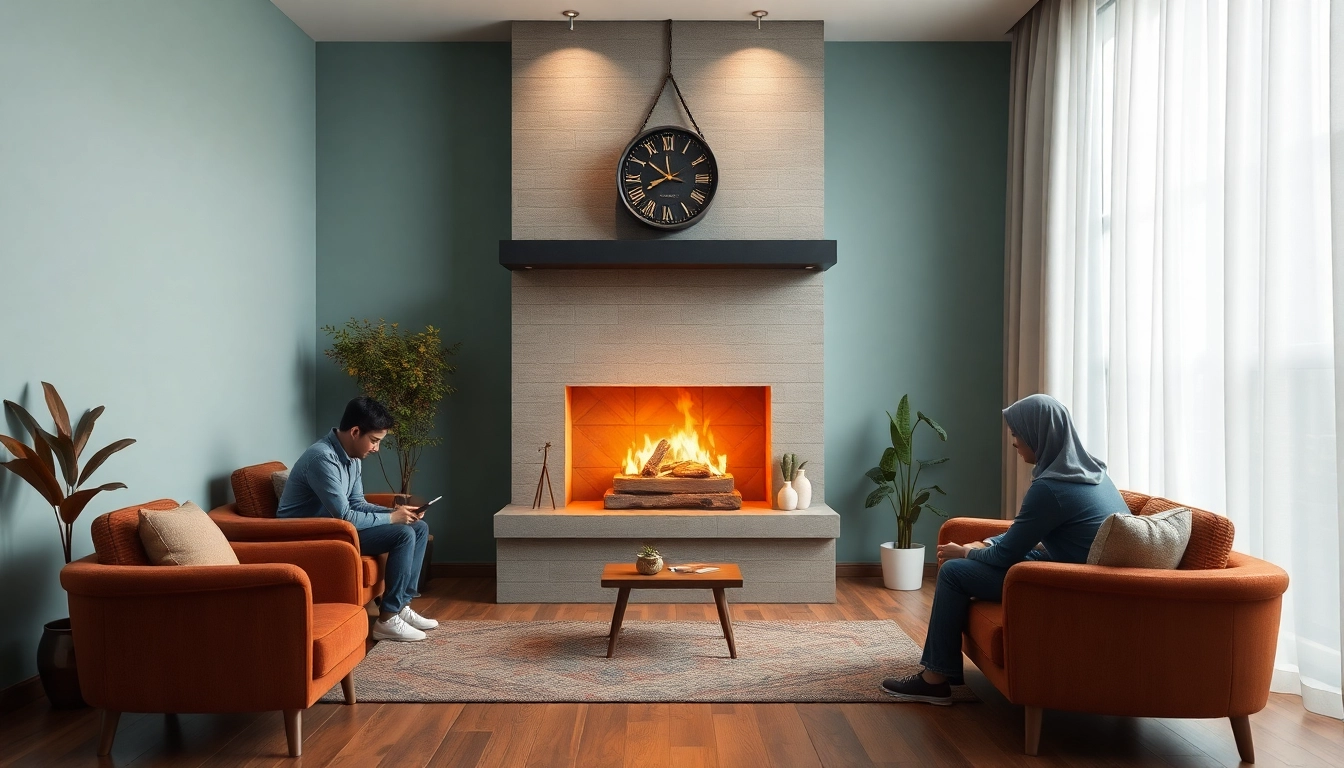
Understanding Liquid Packaging Machines
In the realm of packaging technologies, Liquid Packaging Machine Supplier plays a pivotal role in ensuring that liquid products are efficiently and securely packaged for a wide range of industries. Liquid packaging machines are integral in maintaining the quality, safety, and presentation of liquid products, from beverages and pharmaceuticals to chemicals and cosmetics. This article explores the intricacies of liquid packaging machines, the benefits of choosing the right supplier, an overview of leading machine suppliers, installation and setup processes, and future innovations in the industry.
What are Liquid Packaging Machines?
Liquid packaging machines are specialized equipment designed for filling, sealing, and packaging liquids into various container types such as bottles, pouches, and cartons. These machines can operate in fully automated, semi-automated, or manual modes, catering to different production needs. They are engineered to handle a diverse range of liquid products, including water, juices, sauces, creams, and pharmaceuticals. Key functionalities include:
- Filling precision to avoid wastage and ensure uniformity.
- Sealing mechanisms to prevent leakage and contamination.
- Labeling and coding capabilities to enhance product identification.
- Integration with other equipment like cappers and conveyors to streamline the production line.
Key Features of Liquid Packaging Machines
When considering a liquid packaging machine, several features should be taken into account:
- Filling Mechanism: Options include volumetric, gravimetric, piston, or pump filling systems, each suited for different types of liquids.
- Speed and Efficiency: Machines vary in their throughput rates; high-speed machines can fill thousands of containers per hour.
- Flexibility: The ability to package different types of containers or products without significant downtime.
- Compliance and Safety Features: Adherence to industry standards and safety regulations is paramount, especially in food and pharmaceutical industries.
Common Industries Using Liquid Packaging Machines
Liquid packaging machines serve a multitude of sectors, including:
- Food and Beverage: For packaging drinks, sauces, and emulsions.
- Pharmaceutical: For liquids, gels, and topical solutions, where contamination risks are high.
- Cosmetic and Personal Care: Including lotions, creams, and liquid soaps.
- Chemical: Packaging for industrial chemicals and household cleaning products.
Benefits of Choosing the Right Supplier
Selecting an appropriate supplier for liquid packaging machines can have far-reaching effects on production efficiency, cost-effectiveness, and product quality. The right choice can lead to significant advantages for businesses.
Quality and Reliability in Liquid Packaging Solutions
A reputable supplier guarantees high-quality machinery that adheres to industry standards and regulations. Reliable technology minimizes downtime and maintenance issues, allowing for more consistent production schedules. When assessing potential suppliers, consider their track record and customer feedback on product performance and reliability.
Custom Solutions Tailored to Your Needs
Every business has unique requirements, from production scale to product type. Top suppliers offer tailored solutions that cater specifically to these needs. Customization might involve:
- Adjustments to filling systems for specific liquid viscosities.
- Custom size options for machinery to fit within existing workflows.
- Integration with existing production technologies for enhanced efficiency.
Support and Maintenance Services Offered
After-sales support is crucial when investing in packaging machinery. Reliable suppliers will provide training, regular maintenance, and easy access to replacement parts. Look for suppliers who offer comprehensive service contracts to maintain optimal performance and extend the lifespan of your machines.
Top Liquid Packaging Machine Suppliers
The market is home to several leading suppliers of liquid packaging machines. Understanding their offerings can help businesses make informed choices.
Comparing Features of Leading Brands
Competitors such as Accutek, Viking Masek, FILAMATIC, and E-PAK Machinery offer a wide range of features that cater to different production needs:
- Accutek Packaging Equipment: Known for its variety of filling systems tailored to different types of liquids.
- iPharmachine: Offers specialized machines for pharmaceutical applications, emphasizing precision and safety.
- Viking Masek: Focuses on efficient bagging solutions for thick creams and gels.
- E-PAK Machinery: Known for robust machinery that integrates filling, capping, and labeling processes.
Customer Reviews and Testimonials
Evaluating customer reviews provides insights into the real-world performance of machines from different suppliers. Positive testimonials often highlight:
- Durability and reliability of machines.
- Exceptional after-sales service.
- Efficient technical support.
Pricing Considerations for Quality Equipment
Investing in quality packaging machinery ought to be viewed through the lens of total cost of ownership rather than mere initial purchase price. Factors such as longevity, maintenance costs, speed efficiencies, and quality of end-product should all weigh heavily in this decision.
Installation and Setup of Liquid Packaging Machines
Proper installation and setup of liquid packaging machines are crucial for ensuring effective operation and maximizing production efficiency. A systematic approach is necessary for best results.
Steps to Proper Installation
Installing a liquid packaging machine involves several critical steps:
- Site Preparation: Ensure that the installation site is clean, level, and free from obstructions.
- Technical Inspection: Validate that all required electrical, plumbing, and compressed air supplies are accessible.
- Machine Placement: Position the machine according to the layout that allows for seamless workflow.
- Connection Setup: Connect all pneumatic, electrical, and water lines according to manufacturer specifications.
- Initial Testing: Run preliminary tests with water or non-hazardous liquids to check for leaks and system integrity.
Common Setup Mistakes to Avoid
Mistakes during setup can lead to inefficiencies or even damage to equipment. Common pitfalls include:
- Ignoring manufacturer guidelines.
- Failure to conduct a pre-installation site survey.
- Skipping calibration of automatic filling settings.
- Underestimating the need for operator training.
Ensuring Efficient Operation After Installation
Post-installation, it is essential to maintain the systems for peak performance. Regular inspections, prompt repairs, and consistent operator training can help in:
- Minimizing downtime.
- Preventing common operational issues.
- Maintaining the quality of packaged products.
Future Trends in Liquid Packaging Technology
The liquid packaging industry continues to evolve with advancements driven by technology and sustainability concerns. Staying ahead of trends can ensure competitive advantage.
Innovations Shaping the Industry
Innovation is at the forefront of liquid packaging machine design. Current trends include the development of machinery that can accommodate a broader range of products and materials, offering improved compatibility and usability. Technologies such as IoT are being integrated into machines for monitoring efficiency and troubleshooting in real-time.
Automation and Smart Technologies
The rise of automation in packaging processes is transforming the industry. Smart packaging machines can communicate with other devices, gather data on production metrics, and provide real-time adjustments to minimize human error.
Sustainability in Liquid Packaging Solutions
As environmental concerns rise, many manufacturers are focusing on sustainable packaging solutions. This includes using eco-friendly materials, reducing waste in the packaging process, and implementing practices that lower carbon footprints.