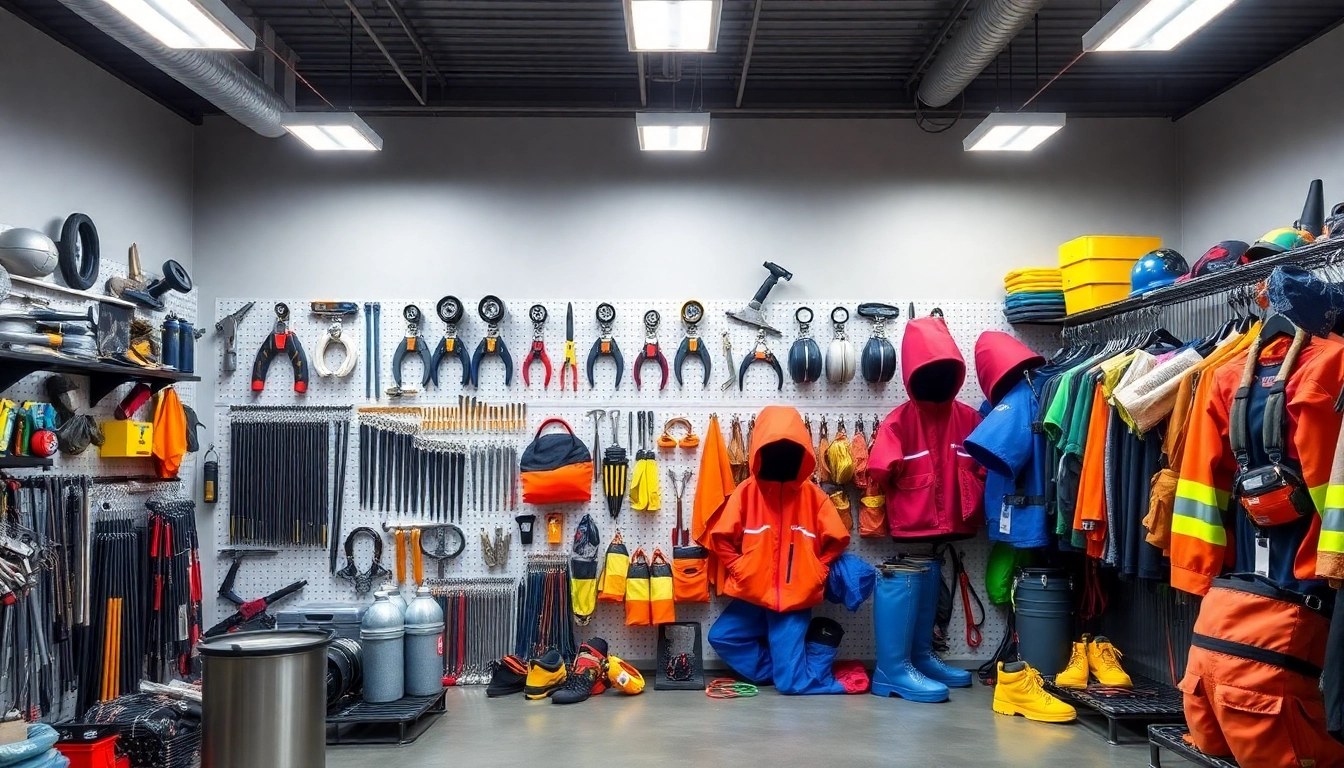
Understanding Welding Supplies: A Comprehensive Overview
Welding is a critical process in various industries, from manufacturing and automotive to construction and art. The right choice of welding supplies can significantly impact the quality of work produced. Understanding the various types of welding supplies and how they are utilized can enhance a welder’s capability and efficiency. This article delves into the kinds of welding supplies available, the prominent brands in the market, and guidance on selecting the right supplies for specific projects.
Types of Welding Supplies
Welding supplies can be categorized into several types, each serving distinct functions during the welding process. The most common types include:
- Welders: Tools that generate the heat needed to melt and join metal parts. The main types include MIG (Metal Inert Gas), TIG (Tungsten Inert Gas), and Stick welders.
- Electrodes: Consumables that carry the current needed to melt and fuse metal parts together. These come in various types based on the welding process.
- Welding gases: Gases such as Argon, CO2, and Acetylene used in different welding processes to shield the weld area and facilitate the welding action.
- Protective gear: Safety equipment such as helmets, gloves, jackets, and boots that protect welders from harmful sparks, heat, and UV radiation.
- Power sources: Equipment that supplies energy to the welder, including transformers, generators, and inverters.
- Welding accessories: Auxiliary tools like clamping devices, welding tables, and wire feed units that enhance the welding process.
Common Brands and Their Features
Several brands dominate the welding supplies market, each known for specific strengths and product lines. Here are a few notable names:
- Miller Electric: Renowned for its durable and reliable welding machines, Miller Electric offers a wide range of MIG, TIG, and Stick welders suitable for both amateurs and professionals.
- Lincoln Electric: Offers a comprehensive line of welding equipment and accessories, known for innovation and reliability in multiple welding applications.
- ESAB: Advanced technology in welding equipment, ESAB is recognized for its high-quality products that enhance welding precision.
- Hobart: This brand is known for its user-friendly welding machines and is particularly favored by hobbyists and DIY enthusiasts.
Choosing the Right Supplies for Your Projects
Selecting the right welding supplies involves understanding your specific project requirements, including the materials to be welded, the type of weld needed, and your skill level. Consult product specifications and seek recommendations based on your project’s scope. It is also crucial to consider factors such as:
- Compatibility: Ensure that all supplies work together seamlessly, particularly electrodes and welding machines.
- Welding Process: Select supplies suited for the intended welding technique (MIG, TIG, or Stick).
- Safety Standards: Invest in protective gear that meets relevant safety standards based on the occupational hazards present.
Essential Tools for Every Welder: Must-Have Equipment
Basic Welding Tools Explained
In addition to welding machines and supplies, certain basic tools are essential for achieving successful welds:
- Welding helmet: A crucial protective feature, welding helmets provide eye protection from harmful UV rays and bright light.
- Welding gloves: High-heat resistant gloves are necessary to protect hands from heat and sparks.
- Chipping hammer: Used to remove slag from welds, this tool promotes better weld visibility and quality.
- Wire brush: It cleans the welded surface to achieve a smooth finish.
Protective Gear You Can’t Ignore
Safety should always come first in welding. Essential protective gear includes:
- Welding Jackets: Made of flame-resistant materials, these jackets protect against sparks and spatter.
- Welding Boots: Sturdy, steel-toed boots protect feet from heavy equipment and hot materials.
- Respirators: Effective in protecting welders from harmful fumes and particulates, particularly in enclosed spaces.
Advanced Equipment for Professional Use
For professional welders, investing in advanced equipment enhances productivity and precision. Key advanced tools include:
- Automatic Welding Machines: These machines streamline projects with enhanced speed and accuracy.
- Multi-Process Welders: Capable of performing various welding techniques, these machines provide versatility for different applications.
- Welding Positioners: Tools to keep workpieces in the correct position to facilitate easier and more accurate welding.
Finding Quality Welding Supplies: Where to Buy
Local Stores vs. Online Suppliers
Deciding where to purchase welding supplies impacts cost, convenience, and availability. Local stores often provide immediate access and expert advice, while online suppliers typically offer broader selections and potentially lower prices. It is essential to evaluate both options based on your needs:
- Local Stores: Great for personal interaction and immediate feedback; ideal for urgent procurement.
- Online Suppliers: Best for comprehensive research on products and comparison shopping for the best rates.
Comparing Prices for Best Deals
When purchasing welding supplies, comparing prices across suppliers is vital to ensure you get the best deal. This involves:
- Researching several suppliers to gauge price ranges for similar products.
- Considering potential shipping costs and taxes when buying online.
- Looking for any available sales, promotions, or discounts.
Understanding Shipping and Return Policies
Before making purchases, be aware of each supplier’s shipping and return policies. Key points to consider include:
- Shipping times and options—how quickly you can expect your supplies to arrive.
- Return policies—understanding how to return a product if it doesn’t meet your needs or is defective.
- Customer support availability to assist with any issues post-purchase.
Best Practices in Using Welding Supplies
Safety Guidelines when Using Welding Tools
Safety is paramount in welding. Following best practices can prevent accidents and enhance effectiveness. Key guidelines include:
- Always wear appropriate protective gear to safeguard against sparks, UV radiation, and fumes.
- Ensure adequate ventilation in the working area to dissipate exhaust and harmful fumes.
- Stay alert and never let distractions interfere while operating welding equipment.
Maintenance Tips for Longevity
Proper maintenance of welding supplies is essential for extending their lifespan and ensuring optimal performance. Some maintenance tips include:
- Regularly clean welding equipment, especially after use, to prevent build-up that can affect functionality.
- Check and replace worn or damaged parts immediately, as this can lead to accidents or faulty welds.
- Store welding tools in a cool, dry place to prevent rust and deterioration.
Understanding Consumables and Their Usage
Consumables, such as electrodes and welding wire, play a significant role in welding quality. It’s important to choose the right type based on your project requirements. Highlights include:
- Understanding the specifications of electrodes that match your welding process.
- Using quality consumables from reputable brands to ensure high-quality welds.
- Tracking usage rates to manage remaining supplies proactively.
Future Trends in Welding Supplies and Technologies
Innovations in Welding Equipment
Technological advancements continue to shape the welding industry. Innovations to watch include:
- Robot-assisted welding: The incorporation of robotics improves precision and efficiency while reducing human error.
- Smart welding technologies: Data-driven solutions that monitor performance and automate settings enhance welding quality.
- Portable welding systems: Designed for convenience, these systems provide flexibility for on-the-go welding projects.
Sustainable Options in Welding Supplies
The focus on sustainability is growing within the welding supplies sector. Innovations include environmentally friendly consumables and energy-efficient equipment, with benefits such as:
- Reduced waste through recycling programs for welding consumables.
- Lower energy consumption from new welding machines, leading to reduced operational costs.
How Technology is Shaping the Future of Welding
Welding is witnessing an evolution driven by advancements in technology, including:
- 3D printing: Integrated with welding processes, this technology enables the creation of complex structures more efficiently.
- Augmented Reality (AR): AR training tools provide comprehensive education for new welders, improving skills through simulated experiences.
- IoT (Internet of Things): Connected machinery that offers real-time monitoring and data collection to refine operational efficiency.