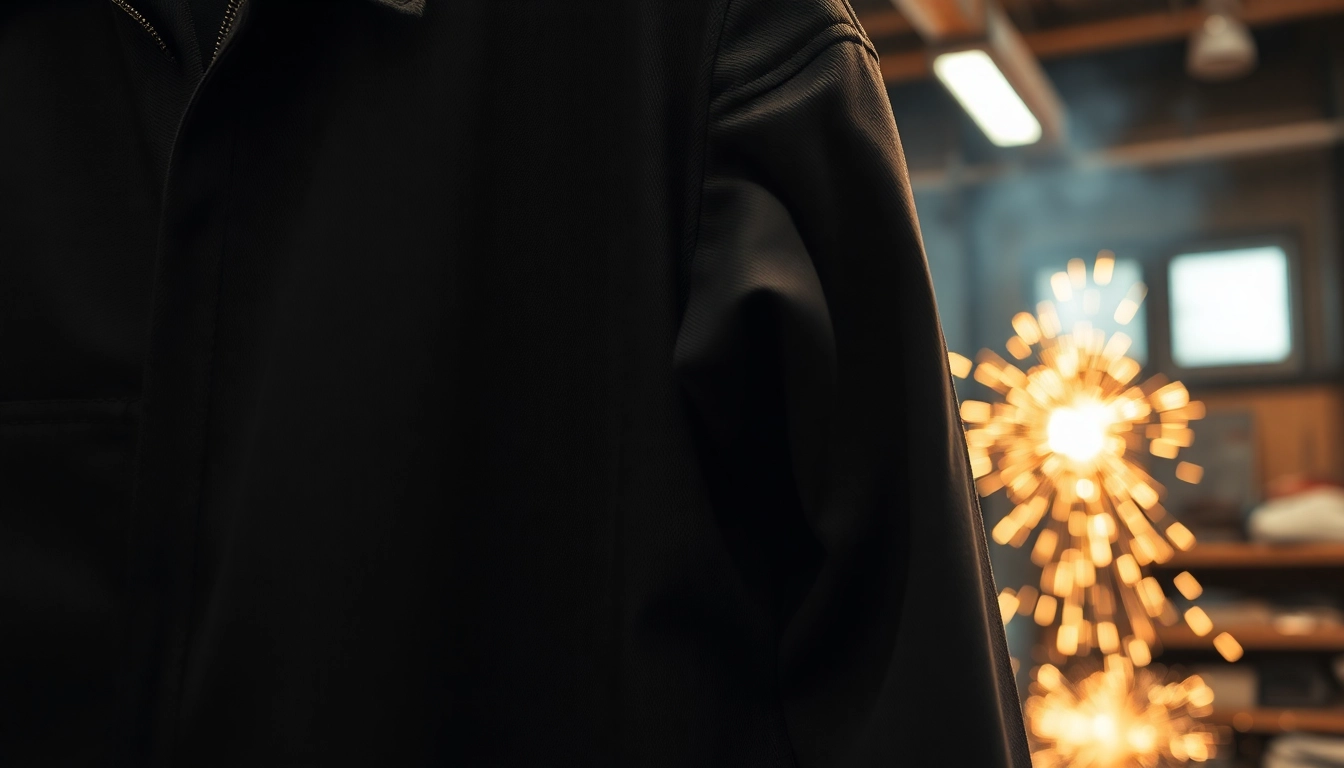
Understanding Welding Jackets
A welding jacket serves as an essential piece of safety apparel for those working in the welding industry. These jackets are specifically designed to protect welders from the numerous hazards present in their work environment, including heat, sparks, and spatter. With a variety of options available, understanding the intricacies of welding jackets is crucial for selecting the right one for your needs.
What is a Welding Jacket?
A welding jacket is typically made from materials that are flame-resistant or flame-retardant, ensuring a protective barrier against extreme temperatures and flying debris. Most commonly, these jackets are crafted from cotton treated with flame-retardant chemicals, leather, or synthesized materials that boast a high resistance to fire. The primary function of these jackets is to shield the welder’s body from harmful elements while maintaining comfort during prolonged periods of use.
Key Features of a Quality Welding Jacket
When selecting a welding jacket, several features should be prioritized:
- Flame Resistance: A reputable jacket must meet the standards set by regulatory bodies like NFPA (National Fire Protection Association) or OSHA (Occupational Safety and Health Administration).
- Durability: It should withstand the mechanical stresses associated with welding tasks. Look for reinforced stitching and high-quality zippers.
- Comfort and Fit: A balance between protection and comfort is essential. Jackets should be fitted without being restrictive, allowing for ease of movement.
- Length: Longer jackets can provide more comprehensive coverage, protecting the wearer from spatter and heat.
- Additional Protective Features: Features such as flap-covered pockets to prevent sparks from entering and adjustable cuffs can enhance protection.
Importance of Flame Resistance in Welding Clothing
The significance of flame resistance cannot be overstated in the realm of welding. Fabric that is not adequately flame-resistant can ignite quickly, leading to severe injuries. Flame-resistant jackets limit the intensity and time of exposure to flames or heat and are critical in protecting the welder’s skin and avoiding serious burns. When choosing a welding jacket, welders must pay close attention to the fabric composition and whether it complies with industry safety standards.
Types of Welding Jackets
Welding jackets come in various styles and materials, each designed to suit different welding processes and personal preferences. Understanding these types will help you select a jacket that aligns best with your requirements.
Leather Welding Jackets: Pros and Cons
Leather jackets are often regarded as the traditional option in welding apparel. They provide outstanding durability and withstand high temperatures effectively.
Pros:
- Durability: Leather is robust, offering excellent abrasion resistance.
- Heat Resistance: Leather naturally withstands high levels of heat, safeguarding welders from sparks.
- Water Resistance: Leather can repel some moisture, further enhancing its protective qualities.
Cons:
- Weight: Leather jackets can be significantly heavier than fabric options, potentially affecting comfort during long sessions.
- Price: They tend to be more expensive than fabric counterparts, which can be a factor for some welders.
- Breathability: Leather does not breathe as well as some fabrics, which could lead to discomfort in hot conditions.
Cotton vs. Synthetic Welding Jackets
Cotton welding jackets treated for flame resistance are commonly favored for their comfort and breathability. Conversely, synthetic options, like those made from Nomex or Kevlar, offer excellent resistance to heat and flames but may lack the breathable quality of cotton.
Cotton Jackets:
- Comfortable Fit: Cotton tends to be softer and more breathable, providing comfort during extended periods of use.
- Economical: Generally less expensive than leather or synthetic alternatives.
Synthetic Jackets:
- Superior Protection: Often provide better flame resistance and durability compared to treated cotton.
- Lightweight: They tend to be lighter, improving mobility.
Customized and Specialty Welding Jackets
For professional welders, custom or specialty jackets may be appropriate. These jackets can be tailored to meet specific job requirements, such as added padding, reflective striping, or unique ventilation features. Ensuring that your protective gear addresses your occupational hazards and fit can improve safety and comfort substantially while you work.
Choosing the Right Welding Jacket
With a variety of options available, choosing the right welding jacket can be challenging. Understanding your specific needs and the environment in which you work is crucial in making an informed decision.
Factors to Consider: Material, Size, and Fit
When selecting a welding jacket, consider the following:
- Material: Choose the material based on the type of welding you perform and the environmental conditions, such as temperature and humidity levels.
- Size: A properly fitted jacket should allow for a full range of motion. It should not be too loose, as this may allow sparks and debris to enter, nor too tight, which could irritate or restrict movement.
- Fit: Look for adjustable cuffs and necklines that help provide a snug fit while promoting airflow.
Top Brands to Explore for Welding Jackets
Brands such as Miller Electric, Lincoln Electric, and Tillman are recognized in the welding community for their high-quality and reliable protective apparel. These brands offer a range of options, including cotton, leather, and synthetic jackets suited for various applications. It’s advisable to conduct thorough research on these brands to find models that specifically cater to your requirements.
Common Misconceptions About Welding Clothing
Several misconceptions surround welding apparel, including:
- The thicker the better. While thicker jackets often provide increased heat resistance, this can lead to reduced comfort and greater fatigue.
- All fabric is created equal. Not all fabrics offer the same level of flame resistance or durability; hence it is vital to check for certification and standards compliance.
- Welders don’t need special clothing. Wearing regular clothing can severely increase the risk of burns or injuries; specialized apparel is crucial for safety.
Maintenance and Care for Your Welding Jacket
Proper maintenance and care of welding jackets can prolong their lifespan and performance. Therefore, adopting best practices for care is essential.
How to Clean and Maintain Welding Jackets
Always refer to the manufacturer’s instructions for cleaning, as different materials require unique care methods:
- Machine Washing: Most cotton and synthetic jackets can be machine washed, preferably in cold water. Avoid using bleach or harsh detergents that may degrade the material.
- Professional Cleaning: For leather jackets, opt for professional cleaning to maintain their integrity and appearance.
- Drying: Air drying is recommended to avoid shrinking or damaging the fabric. Avoid using a tumble dryer, especially for leather jackets.
- Regular Inspection: Check your jacket regularly for signs of wear and tear, including fraying edges or burns; these can indicate when a replacement is necessary.
Signs It’s Time to Replace Your Welding Jacket
Knowing when to replace your welding jacket is crucial for maintaining safety:
- Visible Damage: Tears, holes, or severe discoloration can compromise your jacket’s protective capabilities.
- Loss of Flame Resistance: If your jacket has been exposed to harsh conditions for an extended period, have it inspected and ensure it meets safety standards.
- Comfort Issues: If the jacket no longer fits properly or is uncomfortable, it may be time to find a new one.
Storage Tips to Enhance Longevity
Proper storage is necessary to maintain your jacket’s integrity:
- Clean Before Storing: Ensure your jacket is clean before packing it away; dirt and contaminants can damage fabric over time.
- Hang, Don’t Fold: Hanging your jacket helps to maintain its shape and prevents creasing or wear.
- Avoid Moisture: Store your jacket in a cool, dry place to prevent mildew or other fabric degradation issues.
Safety Best Practices When Welding
Incorporating best practices into your welding safety routine can enhance the protection provided by your welding jacket.
Integrating Welding Jackets into Your Safety Gear
Always ensure that your welding jacket is just one part of a comprehensive safety outfit. Pair it with:
- Protective Gloves: Use gloves designed for welding to protect your hands from heat and sparks.
- Safety Goggles: Eye protection is vital, as welding produces harmful radiant energy.
- Respiratory Protection: Depending on the welding type, consider a mask or respirator to avoid inhaling harmful fumes.
Common Hazards and How Welding Jackets Protect
Welding introduces specific hazards, including burns from molten metal, UV radiation, and inhalation of hazardous fumes.
- Protection Against Burns: A good welding jacket protects the skin from spatter and heat, significantly reducing the risk of burns.
- UV Protection: Fabric that features flame resistance can also mitigate the effects of ultraviolet radiation.
- Respiratory Hazards: While jackets don’t protect against inhalation, wearing a respirator can prevent exposure to harmful fumes often present during welding.
Real-Life Benefits of Wearing a Quality Welding Jacket
Wearing a high-quality welding jacket can yield several important benefits beyond mere compliance with safety standards:
- Increased Comfort: A well-fitted jacket can reduce fatigue and discomfort, allowing welders to focus on their tasks.
- Enhanced Productivity: By decreasing the likelihood of injuries, welders can work more efficiently and with confidence.
- Long-Term Cost Savings: Investing in a quality jacket may reduce costs associated with injuries and replacements in the long run.